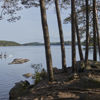
Part of Stena Metall Group
We are a part of the Swedish-based Stena Metall Group, with seven business areas and operations at more than 200 locations in nine countries.
Through research and development, Stena Metall is working to meet the challenges of the future with new, sustainable solutions. The group’s 3,600 employees collaborate closely with partners and customers to create business value while positively impacting the environment and society.